The Pivotal Role of Centrifugal Casting in Manufacturing Bronze Bushing Bearings
Bearing Bronze Solutions – Tailored for Efficiency & Strength
Centrifugal Casting Bronze Bushings, Bearings, and Custom Machining
Centrifugal casting of bronze is a pivotal manufacturing technique for producing high-quality cylindrical components that are integral to various industries, notably in the machine tool sector. This method excels in crafting hollow profiles such as tubes, bushings, bearings, and flange bushings, making it a cornerstone of industrial manufacturing.
Tin Bronze
Bronze Bushings are available in different alloys and compositions.
Tin Bronze Alloys: Known for their strength. (e.g., RG7, C90300, C90500)
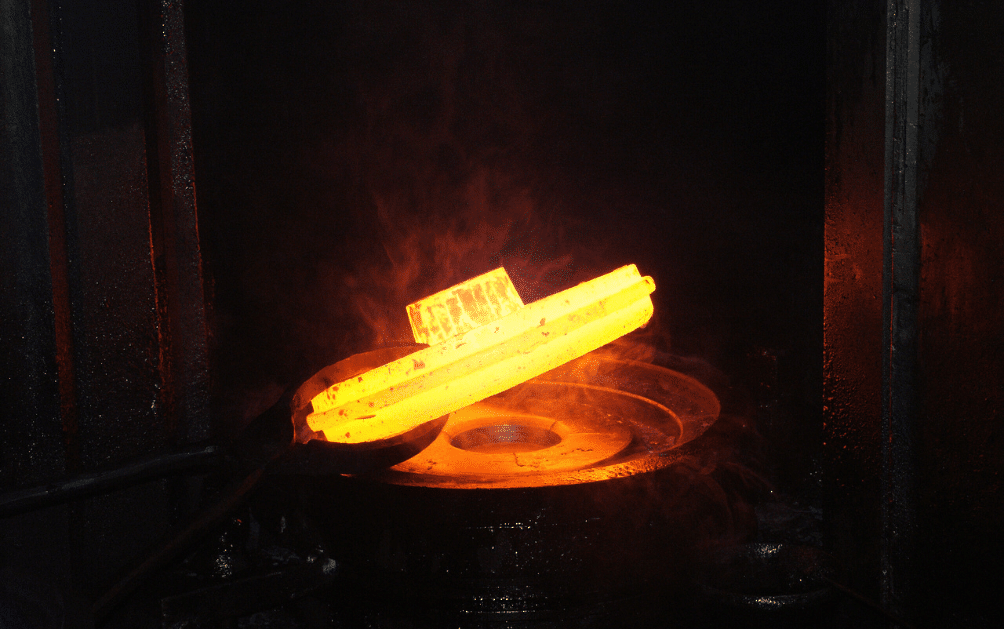
Leaded Bronzes
High Leaded Tin Bronze alloys
Aluminum Bronze Alloys
Special Bronze Alloys
Type Of Bearing
Bearing Bushing Bronze, Instant Pricing & Lead Times,Custom CNC Machining
Centrifugal Cast bronze tubes are available in tin leaded bronze, aluminum bronze, manganese bronze, bronze bushing, alloys and gunmetal.
Custom design, simple or complex. Get a quote. Learn more now.
Centrifugally Cast Bronze Bushing, Large Size Centrifugal Castings for Bronze Bearings
We are particularly valuable for companies offering one-stop solutions for both repair and reverse engineering services in the machine tool sector, enabling the production of high-quality replacement parts and the enhancement of existing components.
Centrifugal casting is a highly effective process for producing large size bronze bearings, offering numerous advantages in terms of quality, durability, and customization.
Large Centrifugal Castings
We specialize in creating large centrifugal castings bronze bushing size , custom centrifugal castings that provide exceptional accuracy and a superior surface finish, catering to a wide range of markets. Contact us to discover more about our offerings!
As always, feel free to contact us at any time to speak with one of our experienced Sales Engineers who can address all your questions and concerns.
Custom Parts Services and Prototyping!
Special Bronze Alloys And Aluminium Bronze Bearing, Search Our Material Alloy
Copper & Bronze Centrifugal Casting
About us
Oversized Bronze Bearing, Bronze Alloy Selection
Sand, Centrifugal, and Continuous Bronze Alloy Casting: The below Bronze Alloy Selection chart showcases our most popular cast bronze alloys, enabling you to compare their chemical and mechanical properties. It also indicates the machinability of each alloy. Additionally, the chart informs you which alloys are readily available in stock at National Bronze Manufacturing, helping you make more informed design decisions for your project.
ALLOY SELECTION CHART | |||||||||||||||||
– Cast Bronze Alloys | |||||||||||||||||
Leaded Tin Bronze
Alloys |
Cross Index | Chemical Composition | Minimum Requirments | Machinability | |||||||||||||
CDA | SAE | AMS | Cu | Sn | Pb | Zn | Tensile (PSI) |
Yield (PSI) |
% Elongation |
BHN @ 500 kg |
|||||||
C83600 | 40 | 4855 | 85 | 5 | 5 | 5 | 36000 | 19000 | 15 | 60 | 84 | ||||||
C84400 | 81 | 3 | 7 | 9 | 30000 | 15000 | 16 | 55 | 90 | ||||||||
C93200 * | 660 | 83 | 7 | 7 | 3 | 35000 | 20000 | 10 | 65 | 70 | |||||||
C93400 | 84 | 8 | 8 | 34000 | 20000 | 8 | 60 | 70 | |||||||||
C93500 | 66 | 85 | 5 | 9 | 2 | 30000 | 16000 | 12 | 60 | 70 | |||||||
C93600 | 80 | 7 | 12 | 1 | 33000 | 20000 | 10 | 60 | 80 | ||||||||
C93700 | 64 | 4842 | 80 | 10 | 10 | 35000 | 20000 | 6 | 80 | 80 | |||||||
Tin Bronze
Alloys |
High Loads – Low Speeds | Cross Index | Chemical Composition | Minimum Requirments | Machinability | ||||||||||||
CDA | SAE | AMS | Cu | Sn | Pb | Zn | Ni | Tensile (PSI) |
Yield (PSI) |
% Elongation |
BHN @ 500 kg |
||||||
C90300 * | 620 | 88 | 8 | 4 | 44000 | 22000 | 18 | 70 | 30 | ||||||||
C90500 * | 62 | 4845 | 88 | 10 | 2 | 44000 | 25000 | 10 | 75 | 30 | |||||||
C90700 * | 65 | 89 | 11 | 40000 | 25000 | 10 | 80 | 20 | |||||||||
C92200 | 622 | 88 | 6 | 1.5 | 4.5 | 38000 | 19000 | 18 | 65 | 42 | |||||||
C92300 | 621 | 87 | 8 | 1 | 4 | 40000 | 19000 | 16 | 70 | 42 | |||||||
C92500 | 640 | 87 | 11 | 1 | 0.5 | 1 | 40000 | 24000 | 10 | 80 | 30 | ||||||
C92700 | 63 | 88 | 10 | 2 | 38000 | 20000 | 8 | 77 | 45 | ||||||||
Manganese
Bronze |
Extreme Loads – | Low Speeds | Cross Index | Chemical Composition | Minimum Requirments | Machinability | |||||||||||
CDA | SAE | AMS | Cu | Zn | Al | Fe | Mn | Tensile (PSI) |
Yield (PSI) |
% Elongation |
BHN @ 500 kg |
||||||
C86200 | 430A | 4862B | 64 | 26 | 4 | 3 | 3 | 90000 | 45000 | 18 | 180 | 30 | |||||
C86300 * | 430B | 63 | 25 | 6 | 3 | 3 | 110000 | 62000 | 14 | 225 | 8 | ||||||
C86500 | 43 | 4860A | 58 | 40 | 1 | 1 | 1 | 70000 | 25000 | 25 | 130 | 26 | |||||
Extreme Loads – Low Speeds | (Corrosive Environments) | Cross Index | Chemical Composition | Minimum Requirments | Machinability | ||||||||||||
CDA | SAE | AMS | Cu | Al | Fe | Ni | Mn | Tensile (PSI) |
Yield (PSI) |
% Elongation |
BHN @ 500 kg |
||||||
C95200 | 68A | 86 | 9 | 3 | 68000 | 26000 | 20 | 125 | 20 | ||||||||
C95300 | 68B | 86 | 10 | 1 | 70000 | 26000 | 25 | 140 | 55 | ||||||||
C95300-HT | 80000 | 40000 | 12 | 174 | 50 | ||||||||||||
C95400 * | 4870 | 83 | 11 | 4 | 85000 | 32000 | 12 | 170 | 60 | ||||||||
C95400-HT | 95000 | 45000 | 10 | 195 | 50 | ||||||||||||
C95500 | 78 | 11 | 4 | 4 | 3.5 | 95000 | 42000 | 10 | 195 | 50 | |||||||
C95500-HT | 110000 | 62000 | 8 | 230 | 40 | ||||||||||||
C95900 * | 82 | 13 | 4 | 1 | 80000 | 40000 | 1 | 255 | |||||||||
C95510-HT * | 4880 | 78 | 10 | 3 | 5 | 1.5 | 105000 | 62500 | 9 | 225 | 50 | ||||||
C63000 * | 4640 | 78 | 10 | 3 | 5 | 1.5 | 90000 | 45000 | 6 | 225 | 30 | ||||||
* Standard Stocked Alloy |
Maintenance Free, Bearing Bushings Bronze Components
In hac habitasse platea dictumst nam quam nunc, blandit vel, luctus pulvinar.